The new TMS 840 generation: the perfect slitter rewinder for narrow rolls
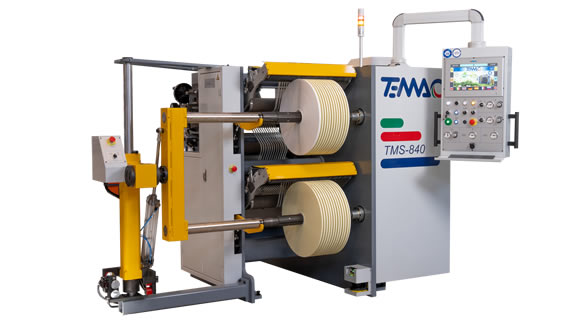
The surprises at Temac never end… the latest in the series is the TMS 840, a compact slitter rewinder designed to process materials such as plastic films, laminates, coextrusions, as well as paper and aluminum, producing thin and narrow rolls.
The applications, as well as the materials it can process, are many: from the labelling sector to automotive, from hygiene and medical to cosmetics.
The machine is equipped with three high-efficiency A.C. asynchronous vector motors (digital flux vector inverters) with low energy consumption thanks to the latest-generation digital vector inverters.
Two of these, operating independently, control the winding torque and individually manage each rewind station through a 15.6” full-color industrial touchscreen Panel PC. This allows for maximum flexibility combined with extreme precision in tension control on the rolls being processed, in line with diameter and speed variations of the machine.
Standard features include:
PLC (programmable logic controller with on-board ETHERNET connection for machine status monitoring and remote service) with HMI interface on IP65 fanless industrial Panel PC (ASEM–ROCKWELL AUTOMATION), 15.6” touchscreen, 4GB RAM, Intel 2.0GHz QuadCore with Windows10 IoT 64bit on SSD.
Automatic film tension control via load cells and microprocessor.
Pneumatic splicing table managed by PLC with film clamping jaws and position sensors.
OPG automatic one-way carriage guiding system with variable angle for roll centering and correction during winding.
Operating speed: 500 m/min.
Circular knife cutting system.
Narrow slits down to a minimum of 8 mm
This new slitter stands out for several features, most notably its ability to slit strips down to just 8 mm wide, and rewind the material on special plastic mandrels.
The machine also features a double set of rewind shafts: both expanding and friction shafts.
In general, expanding shafts are valued for their higher load capacity: the shaft does not flex even when handling particularly heavy material, ensuring flawless winding and straight rolls.
Specifically, the machine comes with two pneumatic expanding rewind shafts with self-centering strips/sectors, designed for cores with an internal diameter of 76.2 mm +0/+0.6 mm (3”).
An independent pneumatic system ensures the management of the rewind shafts both during operation (keeping them firmly in position) and during roll unloading. These functions are PLC-managed to ensure full efficiency of the pneumatic circuit and maximum safety during operation.
Patented special clutches
The friction shafts, interchangeable with the expanding shafts, are equipped with unique patented clutches that enable the machine to handle extremely narrow slits down to 6 mm. These consist of independent 6 mm-wide rings, designed to lock mandrels with 76.2 mm (3”) -0/+0.6 mm internal diameter, using rollers to ensure uniform tension control, directly proportional to the widths of the strips.
With this system, torque control on the processed film is performed by electro-pneumatic transducers controlled by the PLC and transmitted to each clutch via equalized radial pressure according to the widths being processed. In this way, the force applied to the film is automatically controlled by the system. (Maximum load distributed over the full working width of each friction shaft = 200 kg.)
These special clutches are patented: the patent allows the use of rollers instead of balls in the friction rings to lock the cores. Thanks to optimized geometry, the rollers move freely within the grooves without hitting the edges, ensuring greater core stability on the shaft. Rollers offer better grip, especially on smooth plastic or aluminum cores, and do not damage the inside of the cores, unlike balls. They are also suitable for standard cardboard cores and are manufactured in nickel-plated or stainless steel, precision-turned on Swiss-type lathes.
Minimised set-up times
Another innovative feature of this next-generation TMS 840 is a solution designed to significantly reduce machine downtime during cutting unit setup.
This is achieved with an external knife positioning system, essentially an off-machine frame that solves the challenge of frequent slit and job changes throughout the day.
Without this pre-setting system, set-up times could account for about 40% of processing time—now resolved thanks to a specially designed drawer system for the cutting unit, with a second support carriage that allows complete extraction and removal of the circular knife system for replacement with one that is already pre-set.
The good news is that this solution could also be developed for other TEMAC slitter models.